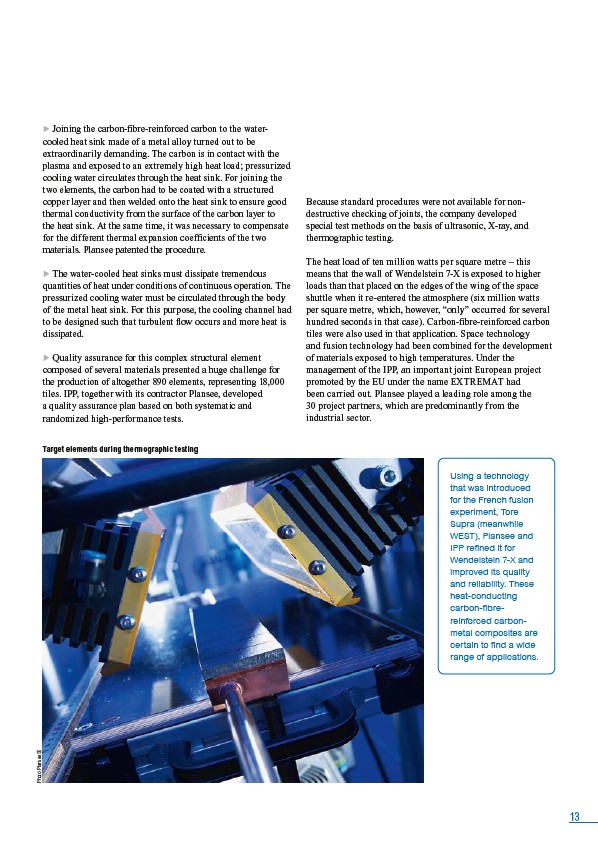
13
▶ Joining the carbon-fibre-reinforced carbon to the watercooled
heat sink made of a metal alloy turned out to be
extraordinarily demanding. The carbon is in contact with the
plasma and exposed to an extremely high heat load; pressurized
cooling water circulates through the heat sink. For joining the
two elements, the carbon had to be coated with a structured
copper layer and then welded onto the heat sink to ensure good
thermal conductivity from the surface of the carbon layer to
the heat sink. At the same time, it was necessary to compensate
for the different thermal expansion coefficients of the two
materials. Plansee patented the procedure.
▶ The water-cooled heat sinks must dissipate tremendous
quantities of heat under conditions of continuous operation. The
pressurized cooling water must be circulated through the body
of the metal heat sink. For this purpose, the cooling channel had
to be designed such that turbulent flow occurs and more heat is
dissipated.
▶ Quality assurance for this complex structural element
composed of several materials presented a huge challenge for
the production of altogether 890 elements, representing 18,000
tiles. IPP, together with its contractor Plansee, developed
a quality assurance plan based on both systematic and
randomized high-performance tests.
Because standard procedures were not available for nondestructive
checking of joints, the company developed
special test methods on the basis of ultrasonic, X-ray, and
thermographic testing.
The heat load of ten million watts per square metre – this
means that the wall of Wendelstein 7-X is exposed to higher
loads than that placed on the edges of the wing of the space
shuttle when it re-entered the atmosphere (six million watts
per square metre, which, however, “only” occurred for several
hundred seconds in that case). Carbon-fibre-reinforced carbon
tiles were also used in that application. Space technology
and fusion technology had been combined for the development
of materials exposed to high temperatures. Under the
management of the IPP, an important joint European project
promoted by the EU under the name EXTREMAT had
been carried out. Plansee played a leading role among the
30 project partners, which are predominantly from the
industrial sector.
Using a technology
that was introduced
for the French fusion
experiment, Tore
Supra (meanwhile
WEST), Plansee and
IPP refined it for
Wendelstein 7-X and
improved its quality
and reliability. These
heat-conducting
carbon-fibrereinforced
carbonmetal
composites are
certain to find a wide
range of applications.
Target elements during thermographic testing
Photo: Plansee SE