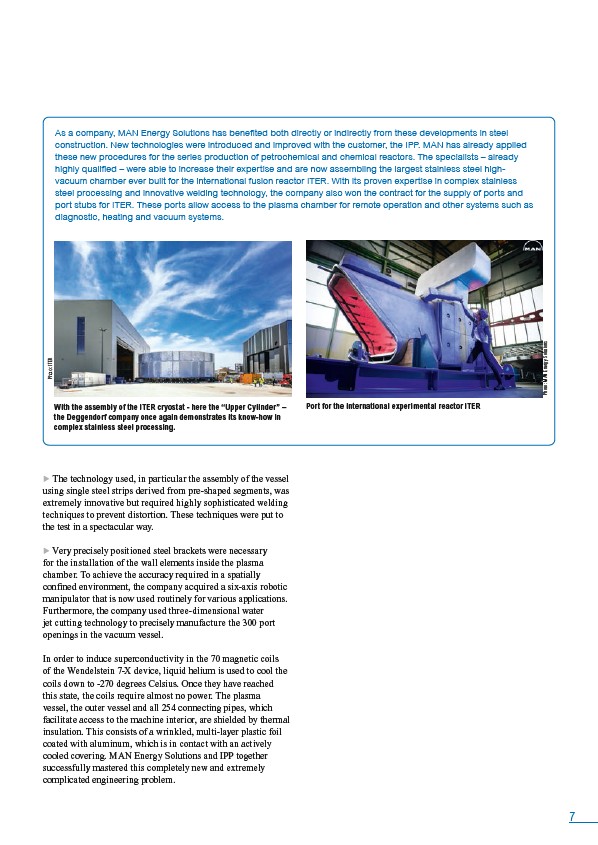
7
As a company, MAN Energy Solutions has benefited both directly or indirectly from these developments in steel
construction. New technologies were introduced and improved with the customer, the IPP. MAN has already applied
these new procedures for the series production of petrochemical and chemical reactors. The specialists – already
highly qualified – were able to increase their expertise and are now assembling the largest stainless steel highvacuum
chamber ever built for the international fusion reactor ITER. With its proven expertise in complex stainless
steel processing and innovative welding technology, the company also won the contract for the supply of ports and
port stubs for ITER. These ports allow access to the plasma chamber for remote operation and other systems such as
diagnostic, heating and vacuum systems.
Port for the international experimental r With the assembly of the ITER cryostat - here the “Upper Cylinder” – eactor ITER
the Deggendorf company once again demonstrates its know-how in
complex stainless steel processing.
▶ The technology used, in particular the assembly of the vessel
using single steel strips derived from pre-shaped segments, was
extremely innovative but required highly sophisticated welding
techniques to prevent distortion. These techniques were put to
the test in a spectacular way.
▶ Very precisely positioned steel brackets were necessary
for the installation of the wall elements inside the plasma
chamber. To achieve the accuracy required in a spatially
confined environment, the company acquired a six-axis robotic
manipulator that is now used routinely for various applications.
Furthermore, the company used three-dimensional water
jet cutting technology to precisely manufacture the 300 port
openings in the vacuum vessel.
In order to induce superconductivity in the 70 magnetic coils
of the Wendelstein 7-X device, liquid helium is used to cool the
coils down to -270 degrees Celsius. Once they have reached
this state, the coils require almost no power. The plasma
vessel, the outer vessel and all 254 connecting pipes, which
facilitate access to the machine interior, are shielded by thermal
insulation. This consists of a wrinkled, multi-layer plastic foil
coated with aluminum, which is in contact with an actively
cooled covering. MAN Energy Solutions and IPP together
successfully mastered this completely new and extremely
complicated engineering problem.
Photo: MAN Energy Solutions
Photo: ITER