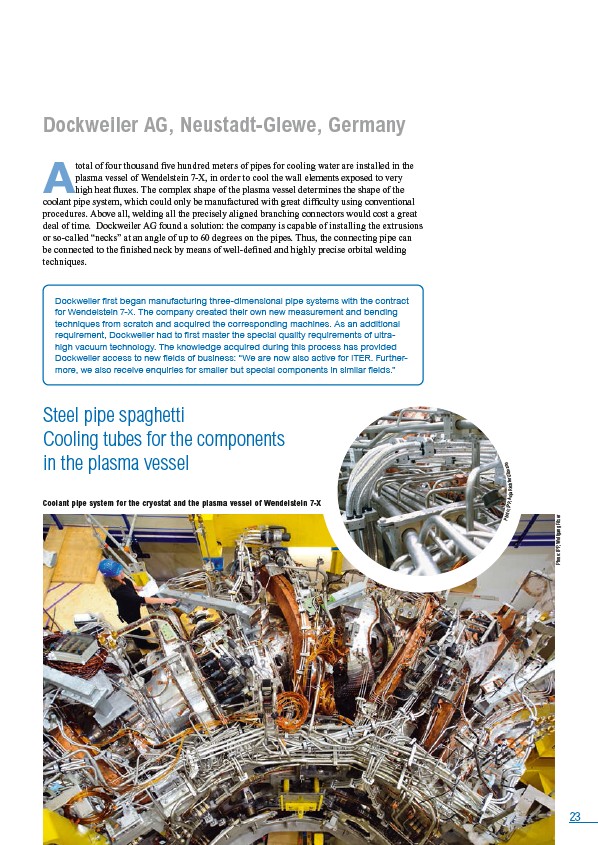
23
Dockweiler AG, Neustadt-Glewe, Germany
A total of four thousand five hundred meters of pipes for cooling water are installed in the
plasma vessel of Wendelstein 7-X, in order to cool the wall elements exposed to very
high heat fluxes. The complex shape of the plasma vessel determines the shape of the
coolant pipe system, which could only be manufactured with great difficulty using conventional
procedures. Above all, welding all the precisely aligned branching connectors would cost a great
deal of time. Dockweiler AG found a solution: the company is capable of installing the extrusions
or so-called “necks” at an angle of up to 60 degrees on the pipes. Thus, the connecting pipe can
be connected to the finished neck by means of well-defined and highly precise orbital welding
techniques.
Dockweiler first began manufacturing three-dimensional pipe systems with the contract
for Wendelstein 7-X. The company created their own new measurement and bending
techniques from scratch and acquired the corresponding machines. As an additional
requirement, Dockweiler had to first master the special quality requirements of ultra-
high vacuum technology. The knowledge acquired during this process has provided
Dockweiler access to new fields of business: “We are now also active for ITER. Furthermore,
we also receive enquiries for smaller but special components in similar fields.”
Steel pipe spaghetti
Cooling tubes for the components
in the plasma vessel
Coolant pipe system for the cryostat and the plasma vessel of Wendelstein 7-X
Photo: IPP, Wolfgang Filser
Photo: IPP, Anja Richter Ullmann