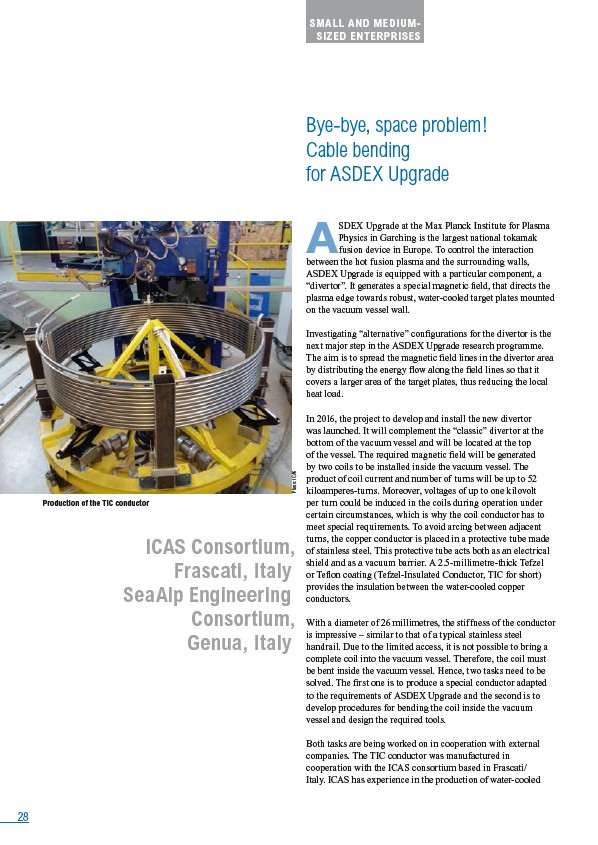
28
SMALL AND MEDIUM-
SIZED ENTERPRISES
Bye-bye, space problem!
Cable bending
for ASDEX Upgrade
ASDEX Upgrade at the Max Planck Institute for Plasma
Physics in Garching is the largest national tokamak
fusion device in Europe. To control the interaction
between the hot fusion plasma and the surrounding walls,
ASDEX Upgrade is equipped with a particular component, a
“divertor”. It generates a special magnetic field, that directs the
plasma edge towards robust, water-cooled target plates mounted
on the vacuum vessel wall.
Investigating “alternative” configurations for the divertor is the
next major step in the ASDEX Upgrade research programme.
The aim is to spread the magnetic field lines in the divertor area
by distributing the energy flow along the field lines so that it
covers a larger area of the target plates, thus reducing the local
heat load.
In 2016, the project to develop and install the new divertor
was launched. It will complement the “classic” divertor at the
bottom of the vacuum vessel and will be located at the top
of the vessel. The required magnetic field will be generated
by two coils to be installed inside the vacuum vessel. The
product of coil current and number of turns will be up to 52
kiloamperes-turns. Moreover, voltages of up to one kilovolt
per turn could be induced in the coils during operation under
certain circumstances, which is why the coil conductor has to
meet special requirements. To avoid arcing between adjacent
turns, the copper conductor is placed in a protective tube made
of stainless steel. This protective tube acts both as an electrical
shield and as a vacuum barrier. A 2.5-millimetre-thick Tefzel
or Teflon coating (Tefzel-Insulated Conductor, TIC for short)
provides the insulation between the water-cooled copper
conductors.
With a diameter of 26 millimetres, the stiffness of the conductor
is impressive – similar to that of a typical stainless steel
handrail. Due to the limited access, it is not possible to bring a
complete coil into the vacuum vessel. Therefore, the coil must
be bent inside the vacuum vessel. Hence, two tasks need to be
solved. The first one is to produce a special conductor adapted
to the requirements of ASDEX Upgrade and the second is to
develop procedures for bending the coil inside the vacuum
vessel and design the required tools.
Both tasks are being worked on in cooperation with external
companies. The TIC conductor was manufactured in
cooperation with the ICAS consortium based in Frascati/
Italy. ICAS has experience in the production of water-cooled
ICAS Consortium,
Frascati, Italy
SeaAlp Engineering
Consortium,
Genua, Italy
Production of the TIC conductor
Photo: ICAS