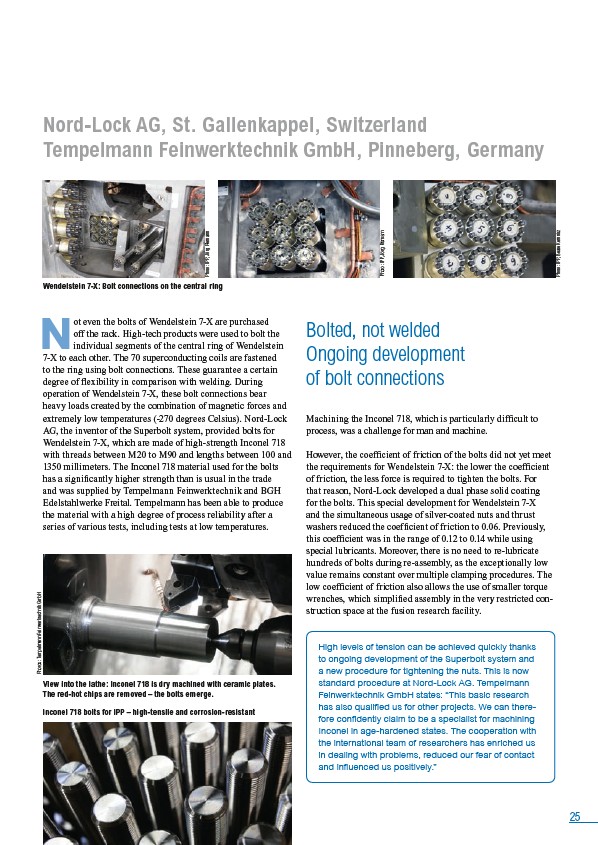
25
Nord-Lock AG, St. Gallenkappel, Switzerland
Tempelmann Feinwerktechnik GmbH, Pinneberg, Germany
Photo: IPP, Jörg Riemann
Not even the bolts of Wendelstein 7-X are purchased
off the rack. High-tech products were used to bolt the
individual segments of the central ring of Wendelstein
7-X to each other. The 70 superconducting coils are fastened
to the ring using bolt connections. These guarantee a certain
degree of flexibility in comparison with welding. During
operation of Wendelstein 7-X, these bolt connections bear
heavy loads created by the combination of magnetic forces and
extremely low temperatures (-270 degrees Celsius). Nord-Lock
AG, the inventor of the Superbolt system, provided bolts for
Wendelstein 7-X, which are made of high-strength Inconel 718
with threads between M20 to M90 and lengths between 100 and
1350 millimeters. The Inconel 718 material used for the bolts
has a significantly higher strength than is usual in the trade
and was supplied by Tempelmann Feinwerktechnik and BGH
Edelstahlwerke Freital. Tempelmann has been able to produce
the material with a high degree of process reliability after a
series of various tests, including tests at low temperatures.
Bolted, not welded
Ongoing development
of bolt connections
Machining the Inconel 718, which is particularly difficult to
process, was a challenge for man and machine.
However, the coefficient of friction of the bolts did not yet meet
the requirements for Wendelstein 7-X: the lower the coefficient
of friction, the less force is required to tighten the bolts. For
that reason, Nord-Lock developed a dual phase solid coating
for the bolts. This special development for Wendelstein 7-X
and the simultaneous usage of silver-coated nuts and thrust
washers reduced the coefficient of friction to 0.06. Previously,
this coefficient was in the range of 0.12 to 0.14 while using
special lubricants. Moreover, there is no need to re-lubricate
hundreds of bolts during re-assembly, as the exceptionally low
value remains constant over multiple clamping procedures. The
low coefficient of friction also allows the use of smaller torque
wrenches, which simplified assembly in the very restricted construction
space at the fusion research facility.
High levels of tension can be achieved quickly thanks
to ongoing development of the Superbolt system and
a new procedure for tightening the nuts. This is now
standard procedure at Nord-Lock AG. Tempelmann
Feinwerktechnik GmbH states: “This basic research
has also qualified us for other projects. We can therefore
confidently claim to be a specialist for machining
Inconel in age-hardened states. The cooperation with
the international team of researchers has enriched us
in dealing with problems, reduced our fear of contact
and influenced us positively.”
Wendelstein 7-X: Bolt connections on the central ring
View into the lathe: Inconel 718 is dry machined with ceramic plates.
The red-hot chips are removed – the bolts emerge.
Inconel 718 bolts for IPP – high-tensile and corrosion-resistant
Photo: IPP, Jörg Riemann
Photo: IPP, Beate Kemnitz
Photos: Tempelmann Feinwerktechnik GmbH