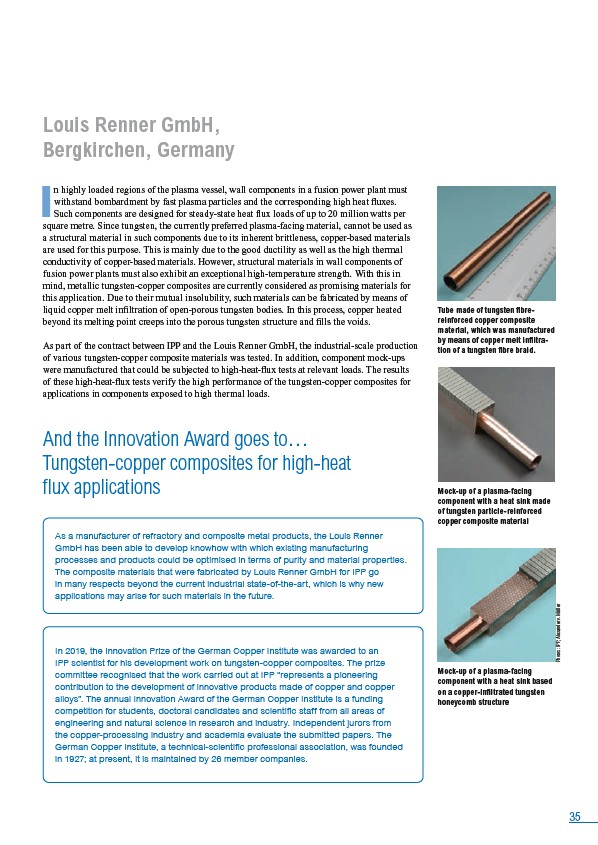
35
Louis Renner GmbH,
Bergkirchen, Germany
In highly loaded regions of the plasma vessel, wall components in a fusion power plant must
withstand bombardment by fast plasma particles and the corresponding high heat fluxes.
Such components are designed for steady-state heat flux loads of up to 20 million watts per
square metre. Since tungsten, the currently preferred plasma-facing material, cannot be used as
a structural material in such components due to its inherent brittleness, copper-based materials
are used for this purpose. This is mainly due to the good ductility as well as the high thermal
conductivity of copper-based materials. However, structural materials in wall components of
fusion power plants must also exhibit an exceptional high-temperature strength. With this in
mind, metallic tungsten-copper composites are currently considered as promising materials for
this application. Due to their mutual insolubility, such materials can be fabricated by means of
liquid copper melt infiltration of open-porous tungsten bodies. In this process, copper heated
beyond its melting point creeps into the porous tungsten structure and fills the voids.
As part of the contract between IPP and the Louis Renner GmbH, the industrial-scale production
of various tungsten-copper composite materials was tested. In addition, component mock-ups
were manufactured that could be subjected to high-heat-flux tests at relevant loads. The results
of these high-heat-flux tests verify the high performance of the tungsten-copper composites for
applications in components exposed to high thermal loads.
And the Innovation Award goes to…
Tungsten-copper composites for high-heat
flux applications
As a manufacturer of refractory and composite metal products, the Louis Renner
GmbH has been able to develop knowhow with which existing manufacturing
processes and products could be optimised in terms of purity and material properties.
The composite materials that were fabricated by Louis Renner GmbH for IPP go
in many respects beyond the current industrial state-of-the-art, which is why new
applications may arise for such materials in the future.
In 2019, the Innovation Prize of the German Copper Institute was awarded to an
IPP scientist for his development work on tungsten-copper composites. The prize
committee recognised that the work carried out at IPP “represents a pioneering
contribution to the development of innovative products made of copper and copper
alloys”. The annual Innovation Award of the German Copper Institute is a funding
competition for students, doctoral candidates and scientific staff from all areas of
engineering and natural science in research and industry. Independent jurors from
the copper-processing industry and academia evaluate the submitted papers. The
German Copper Institute, a technical-scientific professional association, was founded
in 1927; at present, it is maintained by 26 member companies.
Tube made of tungsten fibre-reinforced
copper composite
material, which was manufactured
by means of copper melt infiltration
of a tungsten fibre braid.
Mock-up of a plasma-facing
component with a heat sink made
of tungsten particle-reinforced
copper composite material
Mock-up of a plasma-facing
component with a heat sink based
on a copper-infiltrated tungsten
honeycomb structure
Photos: IPP, Alexander v. Müller