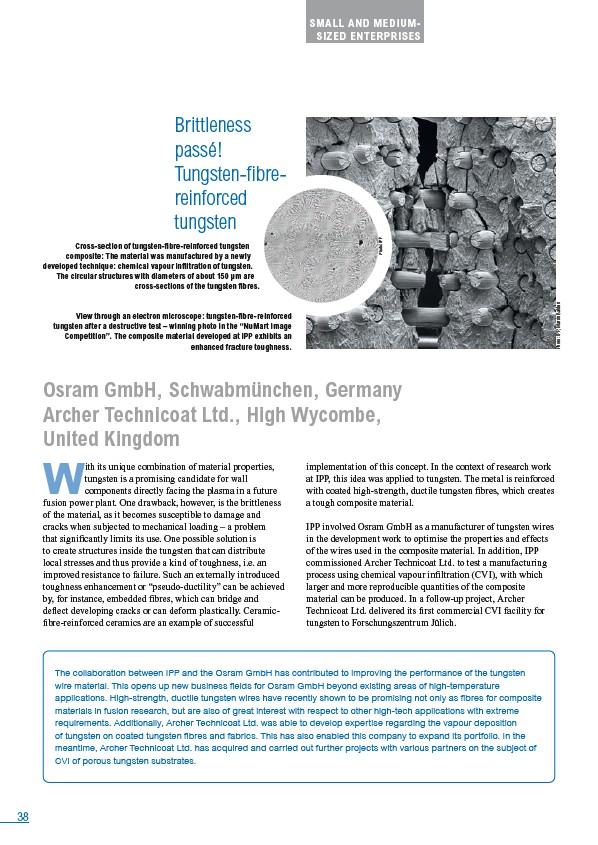
38
Photo: IPP
Brittleness
passé!
Tungsten-fibrereinforced
tungsten
Cross-section of tungsten-fibre-reinforced tungsten
composite: The material was manufactured by a newly
developed technique: chemical vapour infiltration of tungsten.
The circular structures with diameters of about 150 μm are
cross-sections of the tungsten fibres.
View through an electron microscope: tungsten-fibre-reinforced
tungsten after a destructive test – winning photo in the “NuMart Image
Competition”. The composite material developed at IPP exhibits an
enhanced fracture toughness.
Osram GmbH, Schwabmünchen, Germany
Archer Technicoat Ltd., High Wycombe,
United Kingdom
With its unique combination of material properties,
tungsten is a promising candidate for wall
components directly facing the plasma in a future
fusion power plant. One drawback, however, is the brittleness
of the material, as it becomes susceptible to damage and
cracks when subjected to mechanical loading – a problem
that significantly limits its use. One possible solution is
to create structures inside the tungsten that can distribute
local stresses and thus provide a kind of toughness, i.e. an
improved resistance to failure. Such an externally introduced
toughness enhancement or “pseudo-ductility” can be achieved
by, for instance, embedded fibres, which can bridge and
deflect developing cracks or can deform plastically. Ceramicfibre
reinforced ceramics are an example of successful
implementation of this concept. In the context of research work
at IPP, this idea was applied to tungsten. The metal is reinforced
with coated high-strength, ductile tungsten fibres, which creates
a tough composite material.
IPP involved Osram GmbH as a manufacturer of tungsten wires
in the development work to optimise the properties and effects
of the wires used in the composite material. In addition, IPP
commissioned Archer Technicoat Ltd. to test a manufacturing
process using chemical vapour infiltration (CVI), with which
larger and more reproducible quantities of the composite
material can be produced. In a follow-up project, Archer
Technicoat Ltd. delivered its first commercial CVI facility for
tungsten to Forschungszentrum Jülich.
The collaboration between IPP and the Osram GmbH has contributed to improving the performance of the tungsten
wire material. This opens up new business fields for Osram GmbH beyond existing areas of high-temperature
applications. High-strength, ductile tungsten wires have recently shown to be promising not only as fibres for composite
materials in fusion research, but are also of great interest with respect to other high-tech applications with extreme
requirements. Additionally, Archer Technicoat Ltd. was able to develop expertise regarding the vapour deposition
of tungsten on coated tungsten fibres and fabrics. This has also enabled this company to expand its portfolio. In the
meantime, Archer Technicoat Ltd. has acquired and carried out further projects with various partners on the subject of
CVI of porous tungsten substrates.
Photo: IPP, Martin Balden
SMALL AND MEDIUM-
SIZED ENTERPRISES