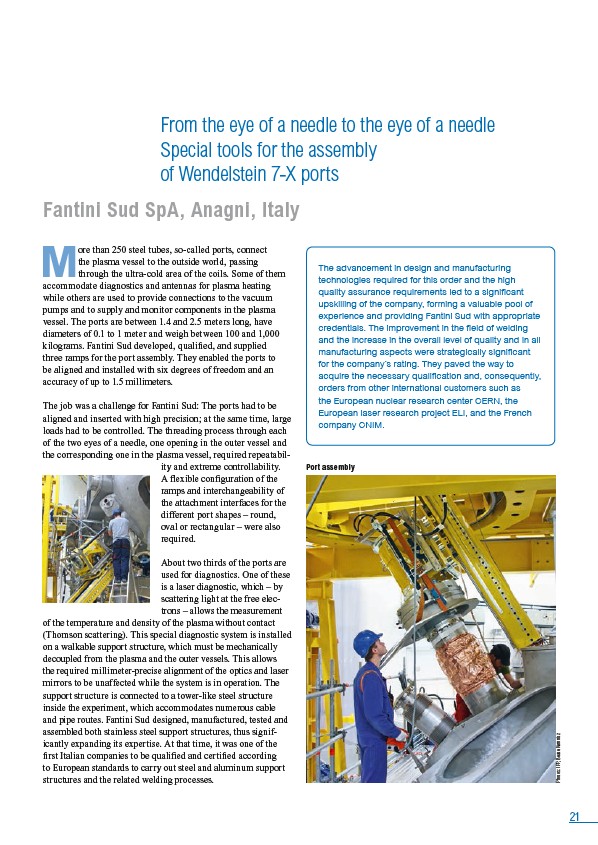
21
From the eye of a needle to the eye of a needle
Special tools for the assembly
of Wendelstein 7-X ports
More than 250 steel tubes, so-called ports, connect
the plasma vessel to the outside world, passing
through the ultra-cold area of the coils. Some of them
accommodate diagnostics and antennas for plasma heating
while others are used to provide connections to the vacuum
pumps and to supply and monitor components in the plasma
vessel. The ports are between 1.4 and 2.5 meters long, have
diameters of 0.1 to 1 meter and weigh between 100 and 1,000
kilograms. Fantini Sud developed, qualified, and supplied
three ramps for the port assembly. They enabled the ports to
be aligned and installed with six degrees of freedom and an
accuracy of up to 1.5 millimeters.
The job was a challenge for Fantini Sud: The ports had to be
aligned and inserted with high precision; at the same time, large
loads had to be controlled. The threading process through each
of the two eyes of a needle, one opening in the outer vessel and
the corresponding one in the plasma vessel, required repeatability
and extreme controllability.
A flexible configuration of the
ramps and interchangeability of
the attachment interfaces for the
different port shapes – round,
oval or rectangular – were also
required.
About two thirds of the ports are
used for diagnostics. One of these
is a laser diagnostic, which – by
scattering light at the free electrons
– allows the measurement
of the temperature and density of the plasma without contact
(Thomson scattering). This special diagnostic system is installed
on a walkable support structure, which must be mechanically
decoupled from the plasma and the outer vessels. This allows
the required millimeter-precise alignment of the optics and laser
mirrors to be unaffected while the system is in operation. The
support structure is connected to a tower-like steel structure
inside the experiment, which accommodates numerous cable
and pipe routes. Fantini Sud designed, manufactured, tested and
assembled both stainless steel support structures, thus significantly
expanding its expertise. At that time, it was one of the
first Italian companies to be qualified and certified according
to European standards to carry out steel and aluminum support
structures and the related welding processes.
The advancement in design and manufacturing
technologies required for this order and the high
quality assurance requirements led to a significant
upskilling of the company, forming a valuable pool of
experience and providing Fantini Sud with appropriate
credentials. The improvement in the field of welding
and the increase in the overall level of quality and in all
manufacturing aspects were strategically significant
for the company‘s rating. They paved the way to
acquire the necessary qualification and, consequently,
orders from other international customers such as
the European nuclear research center CERN, the
European laser research project ELI, and the French
company CNIM.
Fantini Sud SpA, Anagni, Italy
Port assembly
Photos: IPP, Beate Kemnitz